The aluminum extrusion process is a manufacturing method that involves shaping aluminum billets or logs into specific profiles or shapes. Aluminum extrusions have been around for over a century. The process was first developed in the early 1900s by Alfred Wilm, a German metallurgist. Wilm discovered that hot extrusion of aluminum could produce complex shapes with high strength and lightweight, making it ideal for industrial and architectural applications. Read More…
Serving the aluminum extrusions world from Cleveland, Ohio, Talan Products specializes in a range of aluminum extrusion products and services.

Quality Stamping & Tube Corp has been a leader in the aluminum extrusions and metal stamping industries for over 40 years. We attribute our success to our in-house die-making capabilities and wide range of extruded parts. All of our products are manufactured with quick turnaround and made to be high quality and durable. Our aluminum extrusions follow guidelines of up to 6 inches in diameter and...
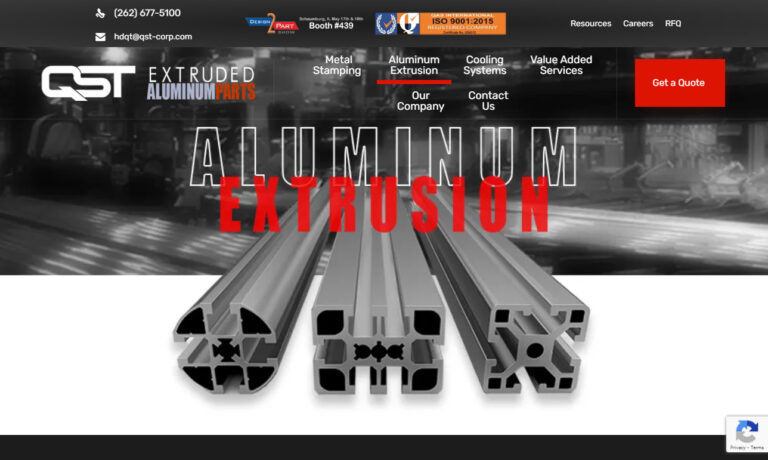
Since 1986, GSH Industries has offered on time delivery and competitive pricing. With over 40,000 square feet of manufacturing, we offer aluminum extrusion products and services.

Dajcor Aluminum is the leading North American supplier of extruded, fabricated/machined, anodized and assembled components to the automotive, renewable energy, transportation, rail, marine, building trades, military, medical architectural and wall partition systems, office furniture, emergency vehicle and consumer product industries. Dajcor is an aluminum extrusion company with complete value add ...
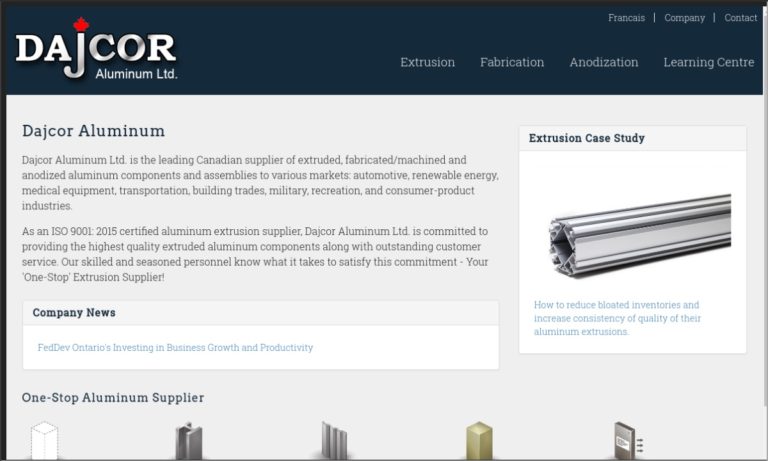
More Aluminum Extrusions Manufacturers
The process of aluminum extrusion was further refined by companies such as Alcoa and Kaiser Aluminum during the 1940s and 1950s. During this time, extrusion technology became more advanced, allowing for the production of more intricate and complex shapes. Additionally, the use of new alloys made it possible to produce extrusions with improved strength and corrosion resistance.
The 1960s and 1970s saw further developments in the use of aluminum extrusions, particularly in the automotive industry. As car manufacturers sought to reduce weight and improve fuel efficiency, aluminum extrusions became an increasingly popular choice for structural components such as body frames and engine parts. In recent years, there has been a growing interest in the use of aluminum extrusions in the renewable energy sector, particularly for solar panel frames and wind turbine components. This has driven further innovation in extrusion technology, with new methods and materials being developed to meet the unique demands of these applications.

The Aluminum Extrusion Process
The process begins with the selection of high-quality billets and involves heating the billet to a specific temperature, then forcing it through a die under high pressure. There are two types of extrusion processes, hot and cold extrusion, each offering its own advantages and applications.
Hot extrusion involves heating the aluminum billet to a temperature of approximately 450°C (850°F) or higher before it is extruded. The heated billet is then forced through a die under high pressure. This process allows for the extrusion of large, complex profiles with precise shapes and dimensions. The high temperature during hot extrusion enhances the aluminum’s plasticity, making it easier to shape and form. Hot extrusion is often employed for manufacturing extrusions that require intricate designs, such as those used in the aerospace and automotive industries. The resulting extrusions have excellent mechanical properties and are well-suited for load-bearing applications.
On the other hand, cold extrusion involves extruding the aluminum billet at room temperature, without the need for preheating. The cold extrusion process offers several advantages, including improved surface finish and dimensional accuracy. It is particularly suitable for producing smaller, simpler profiles with consistent cross-sections. Cold extrusion is often used in applications where tight tolerances and surface quality are critical, such as in the production of electrical components, heat sinks, and precision parts. Additionally, cold extrusion requires less energy compared to hot extrusion, making it a more energy-efficient process.
Both hot extrusion and cold extrusion processes have their place in aluminum extrusion manufacturing, with each process tailored to specific requirements. The choice between the two depends on factors such as the size and complexity of the profile, the desired mechanical properties, dimensional precision, and surface finish. Manufacturers carefully consider these factors when determining which extrusion process to employ in order to achieve the desired outcome for their specific applications.
Various Types of Aluminum Extrusions
Aluminum extrusions come in a variety of types, each designed to fulfill specific functional and aesthetic requirements. Standard profiles are commonly available and widely used in various industries. These profiles typically have regular shapes, such as squares, rectangles, and rounds, and are readily accessible for a wide range of applications. Custom profiles, on the other hand, are specifically tailored to meet unique design requirements. They can be created with intricate and complex shapes, allowing for greater flexibility in product design.
Aluminum extrusions can also be categorized as hollow or solid profiles. Hollow profiles feature an open cross-section, providing a lightweight yet structurally efficient solution. They are often used in applications where weight reduction is critical, such as aerospace and automotive industries. Solid profiles, on the other hand, have a continuous, solid cross-section and are commonly used when enhanced strength and rigidity are required.
Structural and decorative profiles represent another distinction. Structural profiles are designed to withstand heavy loads and provide structural support. They are commonly used in applications such as building and construction, where strength and durability are essential. Decorative profiles, on the other hand, are primarily employed for aesthetic purposes, enhancing the visual appeal of products or architectural elements.
The wide range of types of aluminum extrusions allows manufacturers to select the most suitable profiles for their intended applications, considering factors such as functionality, structural requirements, aesthetics, and material properties. This versatility makes aluminum extrusions a highly adaptable solution in numerous industries, contributing to their widespread usage.
Aluminum Alloy Series’ Used for Extrusions
There are several series of aluminum alloys commonly used in various industries. The most commonly recognized series include the 1xxx, 2xxx, 3xxx, 4xxx, 5xxx, 6xxx, 7xxx, and 8xxx series. Each series represents a specific group of alloys with distinct properties and characteristics. The number before “xxx” denotes the major alloying element or elements present in the alloy. For example, the 1xxx series consists of almost pure aluminum, while the 2xxx series contains copper as the primary alloying element. Each series has its own unique set of properties, making them suitable for specific applications.
Among the various aluminum alloy series, the most commonly used for aluminum extrusions are the 6xxx series. These series are particularly well-suited for extrusion processes due to their excellent combination of strength, formability, and corrosion resistance. The 6xxx series alloys, such as 6061 and 6063, are widely utilized in aluminum extrusions. These alloys feature magnesium and silicon as their main alloying elements, providing good extrudability, weldability, and surface finish. They offer a balance of strength, formability, and corrosion resistance, making them suitable for a wide range of applications in industries like construction, automotive, and consumer goods.
The 5xxx series alloys, including 5052 and 5083, are also commonly employed in aluminum extrusions. These alloys are non-heat-treatable and primarily known for their excellent corrosion resistance. With magnesium as the primary alloying element, the 5xxx series alloys exhibit good formability and weldability. They are often utilized in marine and architectural applications where corrosion resistance is crucial.
While the 6xxx and 5xxx series are the most prevalent for aluminum extrusions, other series like the 7xxx series may also be used in specific applications where high strength is required, such as aerospace and high-performance industries. The choice of alloy series depends on the specific requirements of the application, including strength, corrosion resistance, and formability. Manufacturers carefully select the appropriate alloy series to ensure the desired performance and functionality of the extruded aluminum products.

Limitations of Aluminum Extrusions
One of the limitations of aluminum extrusions is the size and complexity of the extruded profiles. The extrusion process can only produce profiles of certain sizes and shapes, making it difficult to produce intricate designs. Additionally, there is a risk of surface damage during the extrusion process, and distortion or warping during cooling.
Benefits of Aluminum Extrusions
Aluminum extrusions offer numerous benefits that make them a preferred choice in various industries. One of the key advantages is their high strength-to-weight ratio. Aluminum is lightweight compared to other metals, such as steel, while still providing excellent strength. This lightweight property makes aluminum extrusions easier to handle, transport, and install, reducing overall manufacturing and operational costs.
Another significant benefit is the corrosion resistance of aluminum. Aluminum naturally forms a protective oxide layer that prevents corrosion, making it highly durable and suitable for applications exposed to harsh environments or corrosive elements. This corrosion resistance reduces the need for regular maintenance and extends the lifespan of products and structures.
Versatility in design is yet another advantage of aluminum extrusions. The extrusion process allows for the creation of complex and intricate shapes with precise tolerances. Manufacturers can customize profiles according to specific design requirements, resulting in highly functional and aesthetically appealing products. Additionally, aluminum extrusions can be easily fabricated, machined, and joined, further enhancing their versatility.
Energy efficiency is another key benefit. Aluminum has excellent thermal conductivity, allowing for effective heat dissipation. This property is especially valuable in applications such as heat sinks, where efficient thermal management is crucial. Aluminum extrusions can efficiently transfer heat, contributing to energy savings and improved performance in various industries.
Additionally, recyclability is a significant environmental advantage of aluminum extrusions. Aluminum is highly recyclable, and the extrusion process itself generates minimal waste. Recycling aluminum requires significantly less energy compared to primary production, making it an environmentally sustainable choice. This recyclability contributes to the circular economy and reduces the overall carbon footprint.
Overall, the benefits of aluminum extrusions, including their high strength-to-weight ratio, corrosion resistance, design versatility, energy efficiency, and recyclability, make them an ideal solution for a wide range of applications. These advantages have propelled the widespread adoption of aluminum extrusions across industries, ranging from construction and automotive to renewable energy.
Applications of Aluminum Extrusions
Aluminum extrusions have a wide range of applications in various industries, including:
Building and Construction
Aluminum extrusions are commonly used in the construction industry due to their lightweight, high strength, and corrosion resistance. They can be found in window frames, door frames, curtain walls, and roofing systems, among other applications.

Automotive Industry
Aluminum extrusions have been used in the automotive industry for many years, particularly in structural components such as body frames, engine parts, and suspension systems. They provide a lightweight and high-strength solution that helps to improve fuel efficiency and reduce emissions.
Aerospace Industry
Aluminum extrusions are widely used in the aerospace industry due to their high strength-to-weight ratio and corrosion resistance. They are used in the manufacture of aircraft frames, wings, and fuselages, as well as in rocket components and satellites.
Electrical Industry
Aluminum extrusions are commonly used in the electrical industry for busbars, heat sinks, and other applications. Their high thermal conductivity and excellent electrical conductivity make them an ideal choice for these applications.
Medical Equipment
Aluminum extrusions are used in the manufacture of medical equipment such as wheelchair frames, hospital beds, and surgical instruments. They offer a lightweight and durable solution for items that are easy to clean and sanitize.
Renewable Energy
Aluminum extrusions are increasingly being used in the renewable energy sector, particularly for solar panel frames and wind turbine components. They provide a lightweight and strong solution that can withstand harsh environmental conditions.
Consumer Products
Aluminum extrusions are also used in a wide range of consumer products, such as furniture, sporting equipment, and household appliances. They offer a sleek and modern design, as well as being lightweight and durable.
Marine Applications
Aluminum extrusions find extensive use in the marine industry, thanks to their exceptional corrosion resistance, lightweight nature, and high strength-to-weight ratio. They are widely employed in boat building, serving as structural components for hulls, decks, bulkheads, and superstructures.
Architectural Applications
Aluminum extrusions have gained immense popularity in architectural applications due to their versatility, design flexibility, and aesthetic appeal. They are commonly used in windows and doors, offering lightweight structural support and excellent thermal performance.
Choosing the Right Aluminum Extrusion Manufacturer
To ensure you have the most productive outcome when purchasing aluminum extrusions from an aluminum extrusion manufacturer, it is important to compare several companies using our directory of aluminum extrusion manufacturers. Each aluminum extrusion manufacturer has a business profile page highlighting their areas of experience and capabilities, along with a contact form to communicate with the manufacturer for more information or request a quote. Review each aluminum extrusion business website using our patented website previewer to quickly learn what each company specializes in. Then, use our simple RFQ form to contact multiple aluminum extrusion companies with the same form.
Check out our Metal Stampings website
Check out our Investment Castings website