Extruded aluminum is an aluminum alloy that is transformed into shapes with a clear cross-sectional profile for various uses. Read More…
Serving the aluminum extrusions world from Cleveland, Ohio, Talan Products specializes in a range of aluminum extrusion products and services.

Quality Stamping & Tube Corp has been a leader in the aluminum extrusions and metal stamping industries for over 40 years. We attribute our success to our in-house die-making capabilities and wide range of extruded parts. All of our products are manufactured with quick turnaround and made to be high quality and durable. Our aluminum extrusions follow guidelines of up to 6 inches in diameter and...
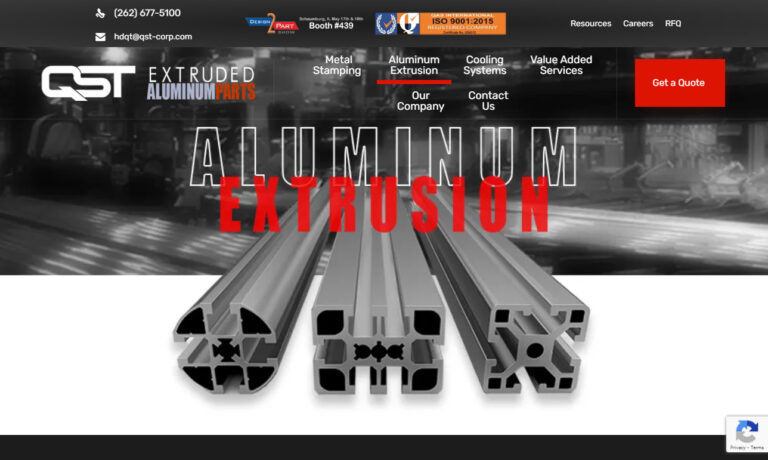
Since 1986, GSH Industries has offered on time delivery and competitive pricing. With over 40,000 square feet of manufacturing, we offer aluminum extrusion products and services.

Dajcor Aluminum is the leading North American supplier of extruded, fabricated/machined, anodized and assembled components to the automotive, renewable energy, transportation, rail, marine, building trades, military, medical architectural and wall partition systems, office furniture, emergency vehicle and consumer product industries. Dajcor is an aluminum extrusion company with complete value add ...
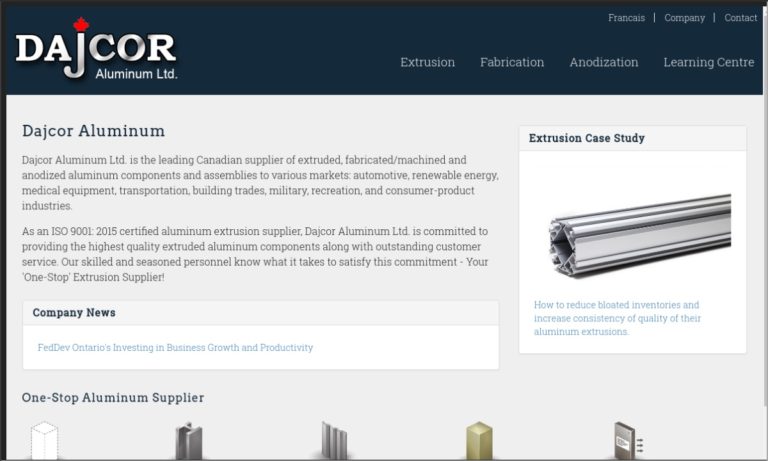
More Extruded Aluminum Manufacturers

Aluminum Extrusion Process
Extruding aluminum is a process similar to creating pasta or running dough through a spaghetti maker. A substantial amount of softened dough is placed in a press and forced through a clearly defined cutout. It exits the other side in the cutout's shape. Extruding aluminum is similar to other metals but on a much larger scale and is done at hotter temperatures. A die maker first builds the piece that the aluminum will be forced through to achieve the desired form.
These dies can be as complex or straightforward as needed, and they can be any combination of solid, hollow, and semi-hollow material. The extrusion mill will then be set up using this die and a billet. A billet is a solid, log-shaped piece of aluminum. It gets soft enough to reshape when heated. The press is filled with the billet and lubrication to prevent the billet from sticking to the other parts. The final shape emerges from the other side of the die as a result of high pressures forcing the aluminum billet through. This new form is uniformly lengthy.

After the final forms are produced, they are often cooled with water jets. These forms are subsequently transferred to a stretcher, straightened, and work-hardened. They are then treated and cut to size. Utilizing specialized ovens, the treatment of aluminum extrusions entails hastening the material's natural aging process. This increases toughness and strength.
Extruded Aluminum Applications
Extruded aluminum is used in many different sectors for various purposes.
Transportation: Aluminum's strength-to-weight ratio makes it perfect for use in cars, trains, boats, and other construction materials. It enables automobiles to be as light as possible. Due to its inherent corrosion resistance, aluminum shields automobiles from environmental exposures, including extreme heat, moisture, and corrosive chemicals like salt in the winter. Due to aluminum’s strength, trucks can transport greater weights. Extrusion components can be assembled to create frames, such as display equipment for shops, trade shows, or portable displays. Additionally, aluminum extrusions work well as picture frames.
Extruded aluminum projects come in a variety of shapes and sizes. Extruded pieces are used in stairways, light fixtures, aluminum panels, and many other things. Other common uses for extruded aluminum are canopies, sunshades, and building facades. For instance, canopies must be able to carry a load in the event of snow but cannot be excessively heavy. In addition, canopies must be visually appealing, much as facades, which aluminum finishes provide. Aluminum extruded parts are a great material option.

Energy: Due to its superior electrical conductivity, double that of copper when compared by weight, aluminum is a great material for power systems in various establishments and industries. It is also frequently used in solar panel mounting systems due to its small weight and low maintenance needs. In addition, aluminum is used in other power constructions because of its durability against strong winds and snow loads.
Military and Defense: Additionally, aluminum extrusions are used in defense-related products like landing mats, ships, and military vehicles. In addition, aluminum extruded parts are used in other high-end military vehicles and common aero planes. The defense industry demands are perfect for its high strength and low weight.
Aerospace: The International Space Station (ISS) is incomplete without aluminum. Truss structures made of the extruded aluminum tube connect the ISS.
Advantages of Aluminum Extrusions
- Affordable – Aluminum is an economical material and less expensive than other methods of producing metal.
- Attractive Finishes – Aluminum can be polished, shined, and anodized.
- Conductive – Aluminum is an excellent electrical conductor.
- Corrosion Resistant – Aluminum creates a thin reactive coating on oxygen to prevent rusting.
- Customization – Aluminum extrusions are the ideal material for product solutions.
- Expansion – Aluminum has a high linear expansion coefficient.
- Highly Reflective – Aluminum is reflective for finishing options and visible light.
- Heat Conductive – Aluminum dissipates heat and is ideal for applications requiring heat shielding.
- Lightweight – In terms of weight, aluminum is roughly one-third that of steel, iron, brass, and copper.
- Low Maintenance – It is naturally corrosion-resistant and does not need a protective covering.
- Malleable – Aluminum is simple to process, extrude, and mold into intricate designs.
- Non-toxic – Aluminum is an easily accessible material that can be used safely.
- Paramagnetic – Aluminum prevents magnetic field interference when utilized in magnet x-ray devices.
- Precise – Aluminum can adhere to tolerances that are exceedingly near or tight.
- Quality- Aluminum provides uniform quality and without mechanical joints when extruded.
- Recyclable- Aluminum is completely recyclable. Aluminum can be recycled indefinitely without compromising its structural integrity. Around 75% of all aluminum created throughout history is still in use.
- Strong – Aluminum extrusions have a high tensile strength range and are sturdy. Aluminum is excellent for applications in cold climates and gets stronger as the temperature drops.
- Time-to-Market- Manufacturing lead times are decreased because aluminum tooling is simpler.
Choosing the Correct Extruded Aluminum Supplier
To make sure you have the most beneficial outcome when purchasing Extruded Aluminum from an Extruded Aluminum Manufacturer, it is important to compare at least 4 Companies using our list of Extruded Aluminum suppliers. Each Extruded Aluminum Manufacturer has a business profile page that highlights their areas of experience and capabilities and a contact form to directly communicate with the manufacturer for more information or request a quote. Review each Extruded Aluminum business website using our proprietary website previewer to get an idea of what each business specializes in, and then use our simple RFQ form to contact multiple Extruded Aluminum companies with the same quote.